BACK TO RESEARCH WITH IMPACT: FNR HIGHLIGHTS
BACK TO RESEARCH WITH IMPACT: FNR HIGHLIGHTS
In 2008, Phillip Dale came to Luxembourg as the first ever Research Fellow of the FNR ATTRACT Programme, which aims to bring excellent young researchers to Luxembourg. It appears that the country is indeed attractive, since the native Brit chose to stay in Luxembourg even after his ATTRACT funding finished at the end of 2012.
As head of the Laboratory for Energy Materials (LEM) in the Physics and Materials Research Unit of the University of Luxembourg (UL), he is doing research on semiconductor materials and their applications in the photovoltaics industry.
In 2010, Dale established a collaboration with the University of Utah in the USA with the help of the FNR’s INTER funding instrument.
The aim of the project, dubbed “LASER” (Laser Annealing of Semiconductor Electrodeposited Reactants), was to improve the quality and production process of thin-film solar cells. The project was a complete success, Dale reports: “We were the first research group worldwide to succeed in reducing the synthesising process for the crucial semiconductors to less than one second,” Dale explains. “In terms of industrial manufacture, speed generally equates to cost savings.”
Baking with the pulsed laser
Thin-film solar cells are about 100 times thinner than conventional silicon-based solar cells. One of their advantages, among others, is that they require less semiconductor material and less energy to manufacture. For synthesising the semiconductor, the elements – usually copper, indium and selenium – are first electrodeposited onto a substrate. At high temperature, this precursor layer is then “baked” in a selenium-vapour-saturated atmosphere.
The Luxembourg scientists wanted to drastically shorten the baking time for this process, also known as annealing. To do so, they fired a laser at the semiconductor using a technique established at the University of Utah, which was made available for the UL team. In this way, they achieved a very high temperature of 800 to 900 degrees Celsius and, with it, an extreme acceleration of the reaction process.
Mike Scarpulla in Utah, an expert in the field of pulsed laser processing of semiconductor materials, and his team have meanwhile studied how structural and electronic defects can be corrected in already finished semiconductors. “That would let us considerably improve the quality of the semiconductors with relative ease,” says Dale.
More pressure, better quality
Currently, the light to electrical power conversion efficiency of the completed devices using the aforementioned laser annealed semiconductors is too low for industrial production, at about 1.5 to 2 percent. The researchers in Utah and Luxembourg are therefore planning a follow-up project, with the primary objective of investigating how that efficiency can be optimised. “We know exactly what needs to be done; we just have to perform the experiments,” says Dale. One idea the scientists have is to increase the selenium vapour pressure during annealing. Initial tests have shown that the quality of the semiconductors increases linearly as the vapour pressure is increased.
Dale relates he has learnt a lot from the project, and not only scientifically. Above all, he found the collaboration with researchers from a different culture especially rewarding: “The colleagues in the USA have an entirely different way of going about things. I found that very exciting,” Dale recounts.
This case study was originally featured in the FNR 2014 Annual Report
RELATED HIGHLIGHTS
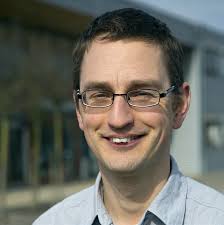
SEE ALSO..
RELATED PROGRAMMES
RELATED PAGES